We believe in being consistent with our deliveries. This means that we are always on time and able to work for your business needs, no matter what they may be.
4 min read
Everything you need to know about robots in manufacturing
Nevatio Team
Oct 11, 2022 11:14:09 AM
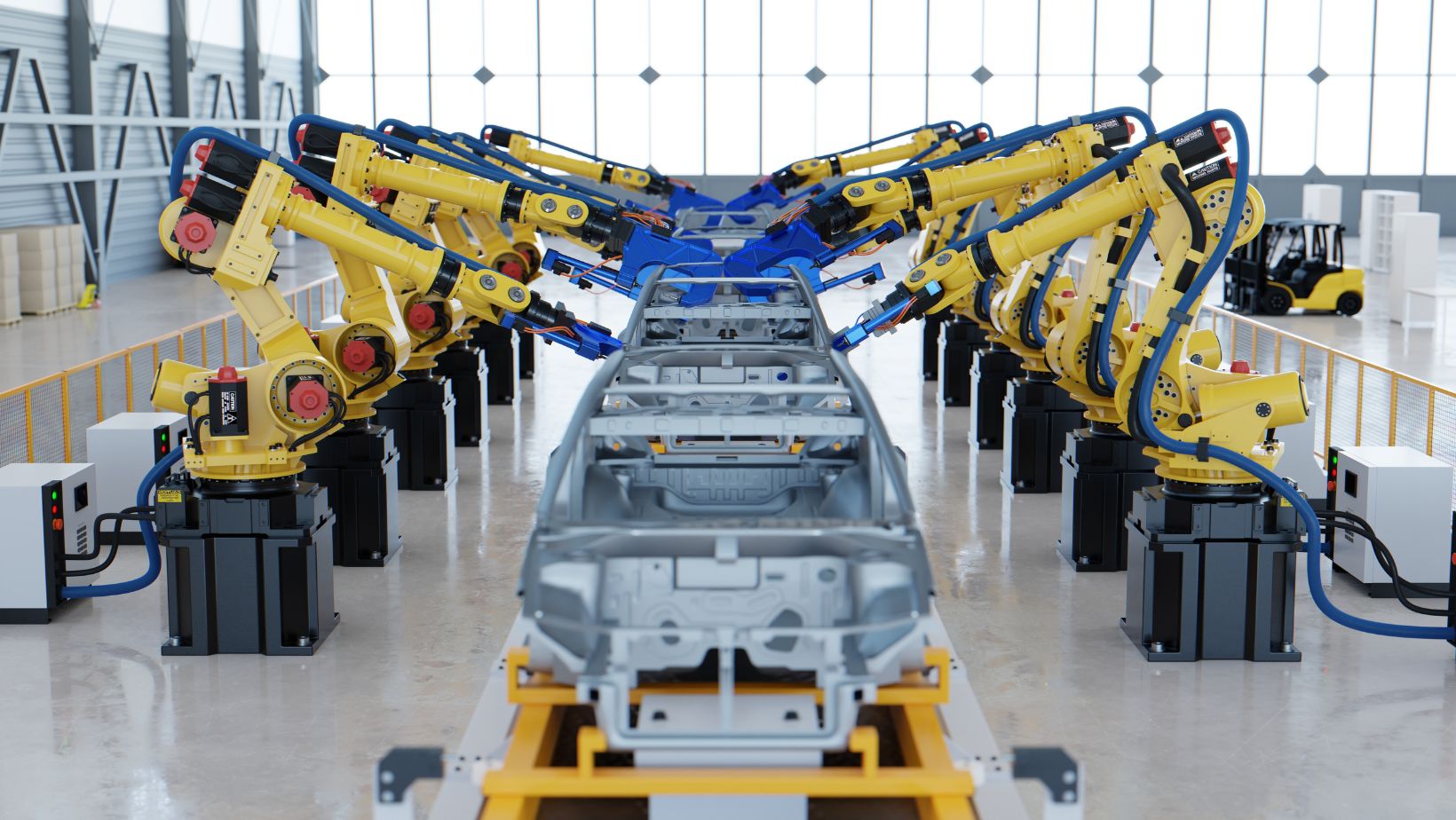
There's no doubt that robots are changing the manufacturing landscape. But what do you need to know in order to take advantage of their capabilities? This blog post will provide an overview of how robots are used in manufacturing, as well as the benefits they can offer your business.
As industrial robots become more prevalent in manufacturing, there is a growing concern over their impact on the workforce. Many people believe that robots will lead to mass unemployment as they take over jobs that are currently done by humans.
However, this may not be the case. While some jobs may be replaced by robots, others will be created as companies find new and innovative ways to use these machines. The future of the workforce is uncertain, but it is clear that robotics will play a significant role in it.
- Why Use Robots in Manufacturing?
- Types of Manufacturing Robots
- How Robotics Are Evolving
- History of Robotics in Manufacturing
- Future of Robotics in Manufacturing
Why Use Robots in Manufacturing?
Robots in manufacturing are increasingly becoming a staple in many factories and plants. They have the ability to improve productivity, while also reducing costs and human error. In addition, they can work tirelessly for long hours without getting tired, and can be programmed to do very specific tasks over and over again with consistent results.
Improve productivity
One of the main reasons manufacturers are increasingly using robots is because they can help to improve productivity. In many cases, a single robot can do the work of several human workers. For example, a welding robot can weld metal components together much faster than a human welder could. This means that more products can be produced in a shorter period of time, which can help to improve a company’s bottom line.
Help to reduce costs
Another reason to use robots in manufacturing is that they can help to reduce costs. In many cases, robots can be purchased for a fraction of the cost of hiring human workers. In addition, robots require less training than human workers, and they don’t need breaks or vacations. This means that companies can save money on labor costs by using robots instead of humans.
Reduce human error
Lastly, robots can help to reduce human error. Humans are susceptible to making mistakes, but robots can be programmed to do tasks perfectly every time. This means that manufacturing companies can rely on robots to produce products that meet the highest standards of quality control.
Types of Manufacturing Robots
There are several types of manufacturing robots, including: assembly robots, welding robots, and material-handling robots.
Assembly robots
Assembly robots are used to put together products. They are typically used in the automotive industry to assemble cars. However, they can also be used to assemble other products, such as computers and electronic devices.
Welding robots
Welding robots are used to weld metal components together. They are typically used in the automotive and aerospace industries. However, they also play a critical role in industrial construction projects, such as petrochemical facilities, power plants, and advanced manufacturing sites - where precise, repeatable welds are essential for safety and system integrity. These types of projects are often led or supported by mechanical contractors, who specialize in systems integration, process piping, and specialty welding services.
Material-handling robots
Material-handling robots are used to move materials around a factory or plant. They are typically used in the food and beverage industry to move products from one location to another. However, they can also be used in other industries, such as the automotive industry. Facilities generating high volumes of packaging waste can improve efficiency and reduce disposal costs by integrating solutions like cardboard balers.
Other manufacturing robots
Robots can be built to accomplish a wide range of activities, and they have the potential to do many of them at a higher level than humans. Repetitive or hazardous work can simply be done by a robot, allowing businesses to produce higher-quality items more regularly.
This versatility is one of the primary reasons that robots have become so popular in the manufacturing industry. Examples of the tasks they can be programmed to perform include:
- Welding materials
- Assembling parts and products
- Cutting and slicing
- Painting products
- Labelling products
- Picking products
- Packing products
- Testing products
- Handling materials
- Handling dangerous goods or waste
- Palletising products
How Robotics Are Evolving
Robots have come a long way since they were first introduced into the manufacturing industry. In the past, they were mostly used for simple tasks, such as welding and assembly. However, they are now capable of much more complex tasks, such as material handling and quality control.
As robots become more advanced, their capabilities will continue to increase. This means that they will eventually be able to replace humans in many manufacturing jobs. While this may seem like a bad thing, it’s important to remember that robots can help to improve productivity and reduce costs. In addition, they can help to reduce human error. As a result, they have the potential to improve the quality of products and make manufacturing companies more efficient.
History of Robotics in Manufacturing
The use of robots in manufacturing is not a new concept. In fact, the first robot was used in a factory back in 1961. This robot, called Unimate, was created by George Devol and Joseph F. Engelberger. It was designed to perform simple tasks, such as welding and assembly.
Since then, the use of robots in manufacturing has increased dramatically. Today, there are over 1.8 million industrial robots in use worldwide. This number is expected to grow to 3 million by 2020.
The growth of robotics in manufacturing can be attributed to several factors. First, the cost of robots has decreased significantly over time. In addition, the capabilities of robots have increased, making them more versatile and able to perform more complex tasks. Finally, the use of robots can help to improve productivity and reduce costs.
Future of Robotics in Manufacturing
In the past seven decades, there have been incredible advancements in robotics and manufacturing. In the 1950s, robots were first introduced onto production lines. Robotics is developing at an amazing pace, with technology, hardware, software, and systems all progressing at a breakneck speed. In this regard, the future of robotics in manufacturing is very promising.
Manufacturing robots are predicted to become more intuitive in the future, relying not just on their programming but also on their ability to react to their surroundings. This is aided by an expansion of the artificial intelligence sector and the development of advanced AI features, which will give robots the capacity to reason for themselves.
Robotics developers, like FANUC, are already creating robots that may learn from their surroundings and from their own actions. This implies that industrial robots will be more self-sufficient, flexible, and require less human involvement in the future.
As manufacturing automation advances, robotic systems will produce goods with higher precision and consistency. This will expand their role into more complex assembly tasks—such as electronics manufacturing, which still often relies on manual labor.
Interested in hiring a Robot?
Let us help you get the right robot to fit your company's needs. Request a quote to get started.
About Nevatio Engineering
Nevatio Engineering is an agile design and engineering consulting team capable of on-demand mechanical and electrical engineering, functional prototyping, engineering documentation, and machine retrofits. Our added knowledge in industry design standards such as ASME, ANSI, ISO, NFPA, NEC and BS allows us to quickly integrate our services with your existing standard design processes, keeping your resources free from unnecessary rework.
We specialize in helping industry leaders solve difficult engineering and design problems. Our mission is to empower our clients with the tools and skills necessary to create solutions to their technical problems. With our expertise, clients can address any technical design problems that stand in their way.
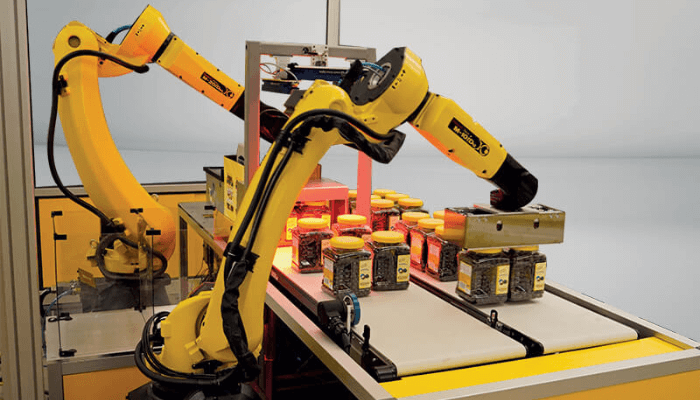
Why Material Handling Automation Is Key to Smarter Production
Material handling automation is transforming the way goods move through modern manufacturing environments. From automated conveyors to robotic...
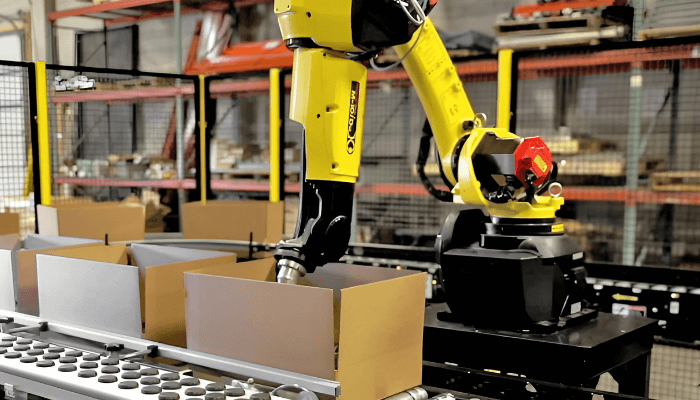
How Logistics Automation Is Reshaping the Modern Supply Chain
As supply chains become more complex and customer expectations rise, businesses are turning to logistics automation to stay competitive. Traditional...
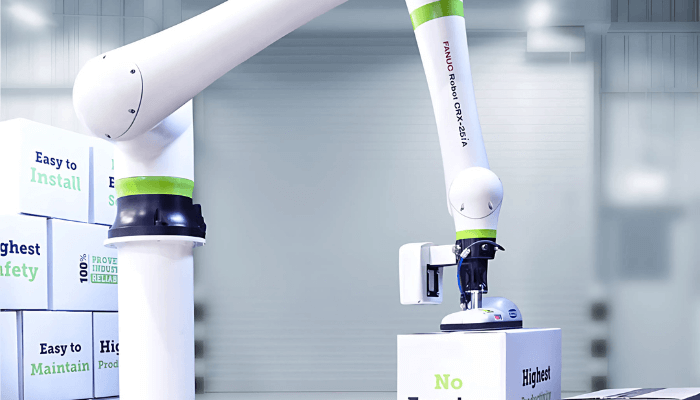
Packaging Automation: Smarter Solutions for Efficient Manufacturing
As production demands rise and labor shortages persist, manufacturers are rethinking how they package and prepare goods for shipment as part of...